By Rajkumar Bhavasar
[Pics. by M.N. Lakshminarayana Yadav]
A few members of the once famed horseshoe maker generation work in cramped spaces on Pulikeshi Road in Tilaknagar, Mysuru. Like the many old structures dotting the area’s landscape that stand amidst high-rises, refusing to change with time’s swift change, these professionals have the unyielding spirit of holding on to the past.
These horseshoe makers — farriers — are carrying on the legacy till their bodies can take the immense physical endurance demanded by the profession. They harbour no illusions and every time their hammers strike the metal, they know their profession has not many takers.
The invention of horseshoes revolutionised ancient means of trade, transportation and warfare. It was necessitated as horses were being exposed to harsh conditions on a daily basis that resulted in breakage, wearing off or damage to their hooves. By providing sufficient protection from sharp objects in the ground and the constant stress of travelling hundreds of miles every day, horses became more useable for longer periods of time.
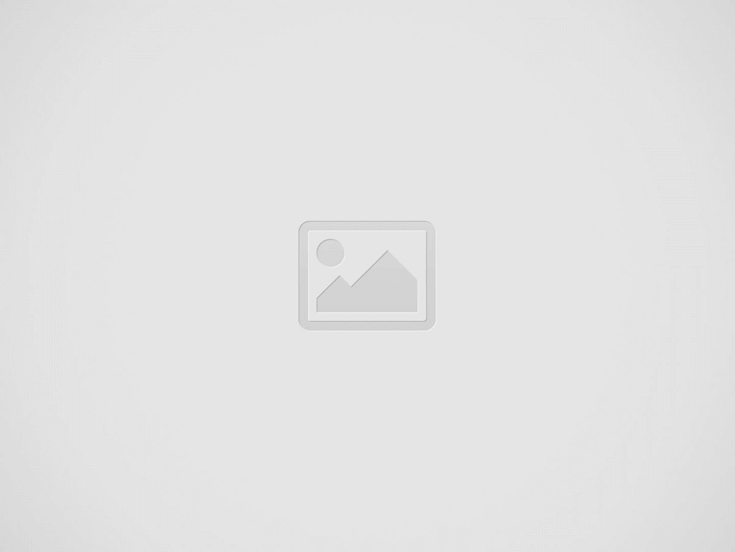
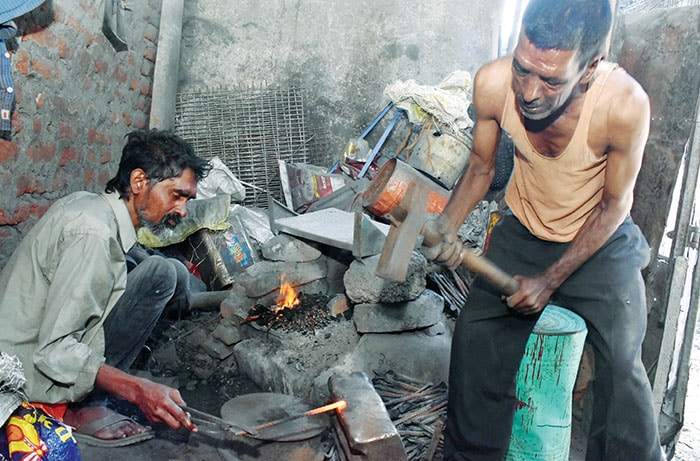
Playing with fire
Moreover, the horses that are equipped with protective foot gear ran faster compared to other horses. However, the work of these farriers is delicate and requires a hard-earned skill. They play with fire and embers to produce that perfect horseshoe to fit the hooves.
Any wrong design or a wrong hole in the horseshoe makes the animal bleed and would lead to a lot of suffering, even death. Although hooves are strong, even stronger than bones, they sometimes developed cracks because of horseshoes. Damage to hooves must be avoided. Hooves have dead tissues and cannot heal themselves. Any crack that reaches the living tissue inside the hoof becomes a spot for infection that takes the life of the animal.
Beating red-hot iron
Farriers on Pulikeshi Road get the iron from scrap yards, heat them, and beat the hot iron to the desired shape. The efforts of three persons are required to make a U-shaped horseshoe. While one person stokes fire to soften the iron, the other person takes a huge hammer and beats the red-hot iron into desired shape.
Excessive heat is involved in the process and these men do not wear any protective gear. After the metal is beaten to shape, holes are drilled into horseshoe to nail them to the hooves. And this is taken care of by another person.
Meagre profits
While U-shaped metal forms the horseshoe for horses, crescent moon shaped shoe is fixed for cows and oxen. These metal pieces wear out quickly and they must be replaced once in two months. Over 20 farriers on Pulikeshi Road work from an old building. There are seven pits where the fire is stoked and horseshoes weighing over 30 kgs are prepared every day in each pit and the income is shared among the three persons.
They do not take a single day off and work tirelessly from 6 am to 3 pm. The horseshoes prepared here is primarily supplied to Nanjangud, Mandya, Handpost, H.D. Kote and surrounding areas. The finished horseshoes are taken in a bag and marketed at designated areas.
Dearth of skilled workers
“Each kilogram of horseshoes is sold at Rs. 150. There is huge demand but we cannot fulfil that as we are facing dearth of skilled workers. Raw materials like iron and coal eat away most of the income and each box of coal costs Rs. 80 and 1 kg of iron costs Rs. 35. Profit is less and we pay a house rent of Rs. 5,000 and we have to maintain the family with the rest of money,” says Fairoz Khan of Aziz Sait Nagar who works as a farrier.
“My grandfather and father were doing this work and I learnt from them. I have not studied beyond second standard and I have been doing this work since 22 years,” he says. In summer, the sun’s heat and the heat generated while making the horseshoe result in boils and even sparks fly to burn their skin. “We don’t know any other work and if we stop this work, our families will go hungry. There is no alternative,” he says.
No one-size-fits all rule
In this skilled work, there is no one-size-fits all rule as hooves are different. Machines cannot produce these horseshoes as there are animals of different age groups. “In the Mysore Race Course, the requirement is for bigger horseshoes which they get from Bengaluru. I have been doing this work since 35 years and I used to work with my father. Even I studied till second standard and I also worked in a scrapyard but returned to this profession,” says 50-year-old Ammanulla Khan.
These farriers also sell crowbars, files, chisels, pliers and tongs. The 88-year-old Abdul Rasheed has been doing this since 50 years. “Earlier, our life was very busy as horse owners, tongawallas and owners of oxen used to line up before our shops for horseshoes. Now, horses have been limited to races and even tongas and bullock carts have been replaced by automobiles,” Rasheed rues.
This post was published on February 23, 2021 6:05 pm